Turning Thoughts to Reality through Plastic Molding
In the current fast-paced manufacturing landscape, companies continuously seeking new approaches to create high-quality items effectively and economically. One method that has gained considerable interest is polymeric inject molding process. It is a flexible production method enables the rapid creation of complex shapes and designs, making a go-to option for industries ranging from automotive to consumer goods.
Through leveraging the advantages of plastic inject forming, businesses can transform their concepts into physical products with precision and swift execution. This technique also facilitates the production of intricate components but in addition ensures uniformity and durability across production runs. As we delve deeper into the world of plastic inject molding process, we will explore how this process can enhance item development and streamline manufacturing operations, aiding businesses realize their concepts to life.
Summary of Injection Molding of Plastics
Injection molding is a commonly employed manufacturing process that converts raw plastic materials into final goods through a sequence of steps. It begins with the warming of plastic pellets until they reach a molten state. This molten plastic is then poured into a custom mold, where it solidifies into a particular shape. The accuracy and speed of this process make it ideal for mass production, allowing manufacturers to create complex shapes with narrow tolerances.
One of the main advantages of plastic injection molding is its flexibility. It can be used to create a wide range of products, from basic components to detailed designs that require multiple colors and materials. This flexibility enables businesses to address diverse customer demands and swiftly respond to market changes. Furthermore, the ability to utilize again molds for various production runs significantly reduces manufacturing costs over time.
The productivity of plastic injection molding also relates to its green impact. Many modern facilities emphasize sustainability by using recycled materials and implementing energy-efficient practices. Additionally, the accuracy of the injection process produces minimal waste, leading to a more sustainable choice in manufacturing. As industries more and more focus on reducing their carbon footprint, plastic injection molding service remains an attractive option for creating high-quality, environmentally friendly products.
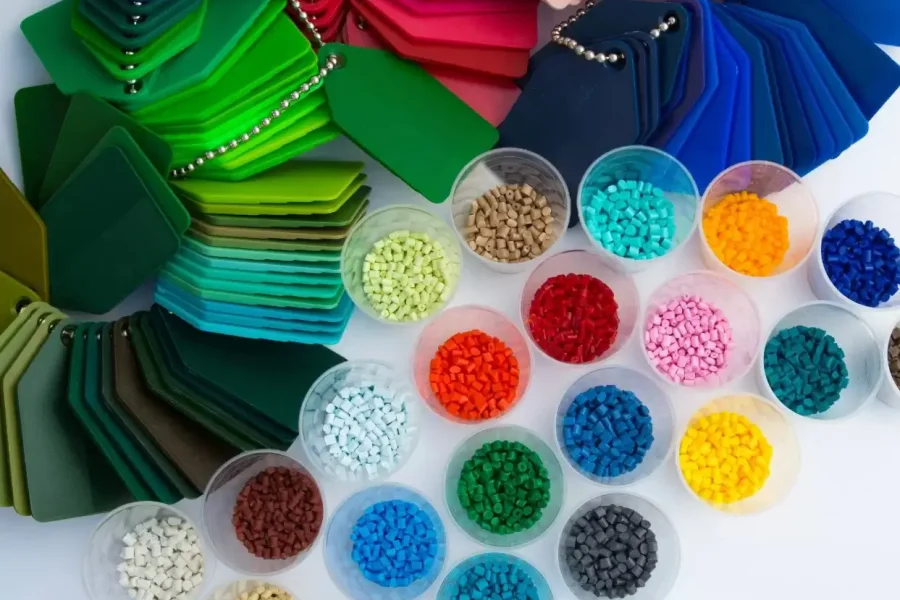
Gains of Plastic Molded Manufacturing Services
Polymer injection solutions offer numerous gains that make them a favored choice for producing various components. One of the primary advantages is the significant efficiency of the manufacturing process. After the mold is formed, it enables for rapid duplication of parts, greatly reducing production time. This efficiency results into lower workforce costs and faster turnaround times, establishing it an excellent option for companies looking to bring their products to the marketplace promptly.
Moreover, polymer molding is recognized for its potential to create intricate shapes and detailed designs with precision. The process allows manufacturers to create parts with high tolerances, guaranteeing that each component meets the required requirements reliably. This accuracy not only improves the standard of the end goods but also limits waste, as molds can be crafted to optimize material usage and reduce scrap.
Lastly, the versatility of substances available for polymer injection contributes to its benefits. A broad range of thermoplastics and thermoset materials can be used, enabling companies to pick the most suitable material for their distinct application. This flexibility permits businesses to create and tailor products to meet diverse market needs, ultimately enhancing their competitive edge in the field.
Applications and Fields Implementing Injection Molding
Plastic injection molding services plays a pivotal part in multiple industries by providing optimized and affordable solutions for producing high-quality plastic components. The automotive industry significantly gains from this process, as manufacturers need precise and robust parts for vehicles, including cabin parts to complex engine elements. Injection molding enables quick production, enabling automotive firms to meet the high demand for parts while ensuring rigorous safety and performance standards.
In the consumer goods area, injection molding is heavily used to manufacture regular products, such as toys, kitchenware, and electronic housings. The versatility of this manufacturing process allows designers to create and supply products in diverse shapes and sizes while maintaining stability and reliability in production. Additionally, the ability to use a broad spectrum of materials further enhances the attractiveness of injection molding for consumer goods.
The healthcare sector is a further key field where plastic injection molding services is crucial. Medical devices, laboratory equipment, and containers for pharmaceuticals often rely on injection-molded parts. This approach supports the production of sterile, lightweight, and durable products, crucial for maintaining patient safety and complying with stringent regulatory requirements. As technology advances, the use of injection molding in healthcare continues to progress, enabling the development of intricate designs and specialized applications.